MathWorks In Racing Technology!
Introduction
ASU Racing team is the current holder of the overall concept class engineering design award in Europe’s most established educational engineering competition: Formula Student UK. The team ranked 5th worldwide in the autonomous driving category. ASU Racing Team actively participates and excels in other international competitions, including:
- Formula Student UK
- Shell Eco-marathon
- EVER – Electric Vehicle Rally

The competition provided us with an ideal opportunity to demonstrate our engineering knowledge and test and improve our capabilities to deliver a complex and integrated product in the demanding environment of a motorsport competition as it challenges us to design, build and race a single seat racing car in one year and we have been participating in FSUK since 2012 with a vision of influencing the automotive industry in Egypt.
The road from design concept to Silverstone track
Thanks to the powerful modeling and simulation software provided by MathWorks. The team was able to follow the model-driven design approach which facilitated overcoming multiple challenges associated with designing a race car as the team had an opportunity to optimize the design and streamline the manufacturing process.

Developed models and simulations:
Throughout their journey, ASU Racing Team has developed a range of models and simulations to enhance the design process of various systems. These tools enable the team to analyze, optimize, and refine their designs, ensuring the highest level of performance and efficiency. Some notable examples of the team’s innovations include:
- Tire model: ASU Racing Team has developed a sophisticated tire model that accurately simulates the behaviour of the tires under different conditions, enabling them to optimize vehicle dynamics and performance.
- Driveline model: By creating a comprehensive driveline model, the team can analyze power transmission, torque distribution, and efficiency, leading to improved overall vehicle performance.
- Suspension vibrational model: ASU Racing Team has developed a simulation that accurately predicts the behavior of the suspension system, allowing for precise tuning and optimization to enhance vehicle stability and handling.
- Brakes model: This model enables the team to simulate and analyze the behavior of the braking system under different scenarios and conditions. By considering factors such as brake pad material, rotor size, and hydraulic pressure.
- Lap time simulation: The team utilizes a lap time simulation tool, which considers various parameters such as vehicle dynamics, powertrain performance, and track conditions. This enables them to strategize and optimize their race performance.
- Powertrain optimization: ASU Racing Team focuses on optimizing the powertrain system, employing simulations to fine-tune engine performance, drivability, and fuel efficiency.
We will break down the process in detail for specific models in the following sections.
Building a Dynamic Simulink Model for a Formula Student car Brake System
To optimize the brake system design, the team realized the necessity of implementing an accurate model that incorporates various vehicle parameters. This comprehensive model would enable an in-depth analysis of the brake system’s performance.
Breaking down the problem
The brake model relies on the tire model as an input and integrates the vehicle’s aerodynamic parameters. The system was divided into several subsystems, including Force Distribution, Rotor Diameters, Locking Time, Master Cylinder Calculation, Adhesion Force Calculation, and Stopping Distance Calculation. Each calculation provided essential outputs that were utilized in subsequent stages.
How did we implement it?
The team collected the necessary information for the model, including static weight distribution and the Mu vs. Slip ratio curve for the tire. By employing weight transfer equations, the required braking force and braking bias ratio were calculated.
Results
The developed model produced several key outputs, including the maximum stopping distance from a given speed, the maximum braking force, and the optimum brake bias. These results enable a thorough understanding of the brake system’s performance and aid in its optimization.
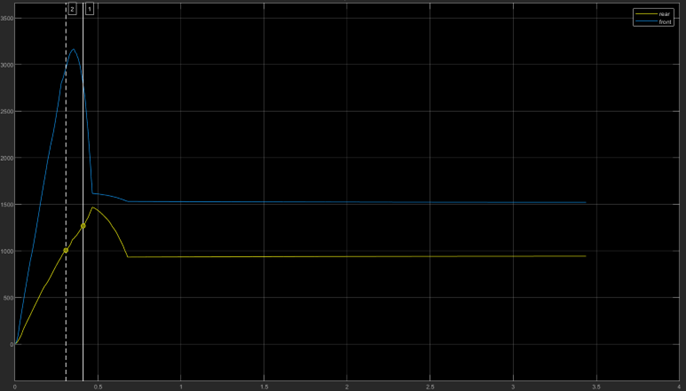
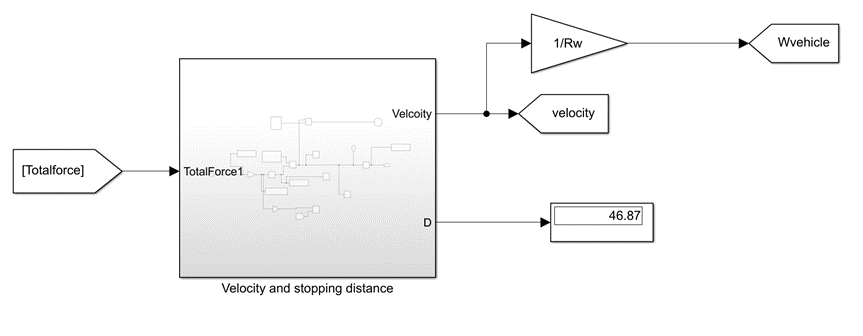
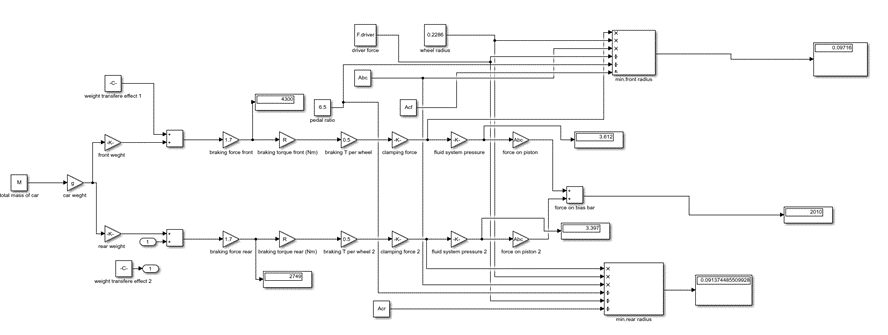
Developing Lap-Time simulation for a Formula Student car using MATLAB.
Designing a high-performance vehicle requires precise tuning and extensive analysis. Recognizing the need for an accurate lap-time simulation, the team embarked on developing their own solution. Existing software options were either expensive or relied on estimations, prompting the team to create a more cost-effective and reliable simulation using MATLAB.
Breaking down the problem
The team needed the simulation to be as accurate as possible to be efficient, also the simulation should be able to output the vehicle parameters among different tracks such as wheel loads, steering angles, throttle and brakes operation, etc.
The team started searching for resources and surveying the optimum software to use, MATLAB being a powerful software able to solve hard mathematical equations was the perfect selection among other software.
How did we implement it?
We started by simplifying the problem by using a quasistatic approach which is a less accurate approach but very good to get into understanding the problem, then we had to analyse the track by getting the maximum speed allowable for the vehicle at each point on the track, the car was them accelerated and decelerated at each point on track with the least speed at each point being the optimum.

To compensate for the reduced accuracy of the quasistatic approach, the team incorporated a full vehicle model, as well as their developed powertrain and tire models. This integration ensured a more accurate simulation compared to freely available software and offered a cost-effective alternative to paid solutions, successfully achieving the team’s objectives.
Results
The developed simulation yielded several valuable outputs, including heat maps of the track and an Excel file detailing the vehicle’s condition at each point (speed, acceleration, slip angle, steering angle, wheel loads, etc.). These outputs were utilized in the fatigue analysis of critical vehicle parts.
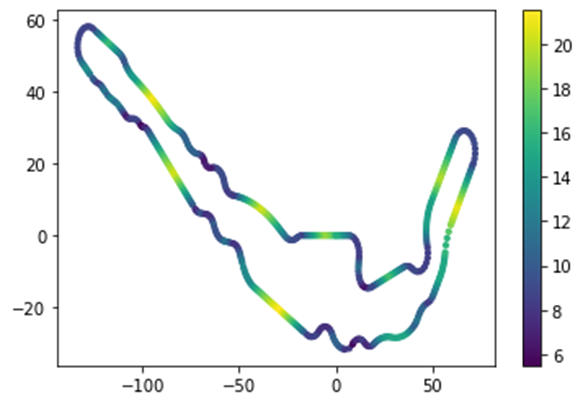
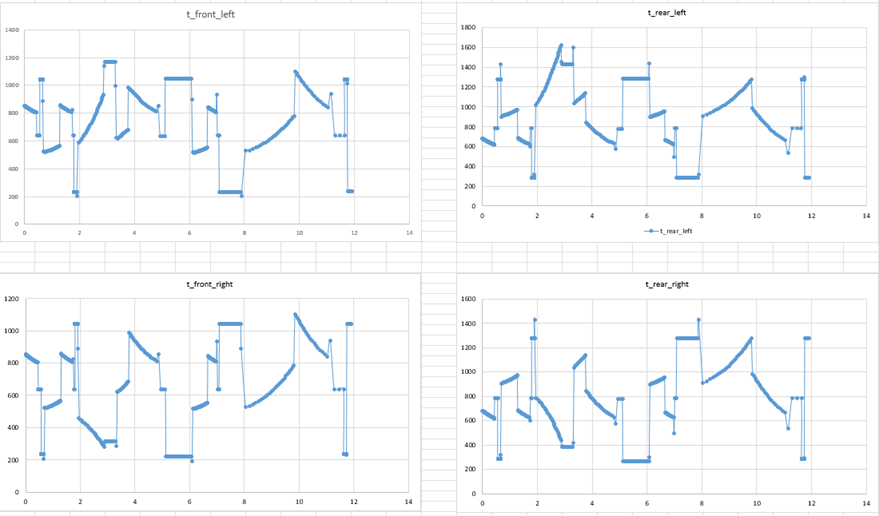
Developing Simulink battery model for a Formula Student car.
Designing a high-performance vehicle requires precise tuning and extensive analysis. The team aimed to estimate vital metrics such as battery capacity, state of charge, and temperature rise on the track.
Breaking down the problem
The team needed to simulate the car’s behavior on the endurance track to estimate its required capacity, SoC, temperature rise, and its power draw at any given point on the track. The initial capacity for the battery was determined by conducting an Optimum lap simulation focused on the endurance event. Subsequently, a Simulink model was developed to validate the results and ensure more reliable decision-making.
How did we implement it?
An equation-based Simulink model is done. Its main input parameter is the velocity-time graph taken from Optimum lap, followed by a series of equations to calculate the required capacity, SoC, and temperature rise. In addition, the Simulink model provided valuable insights for the battery system. It determined the optimal configuration of cells in series and parallel to meet the performance requirements. Furthermore, the model generated crucial data, including the temperature rise during the endurance event, power dissipation, and the required flow rate to minimize the temperature rise within the battery during operation.
Results
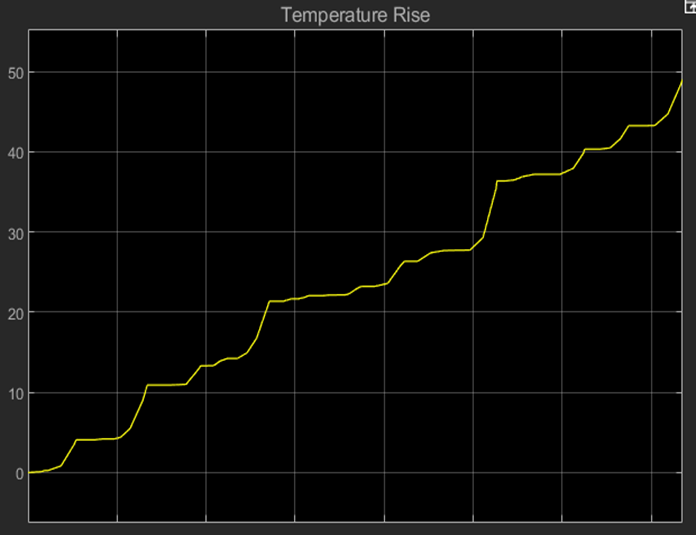
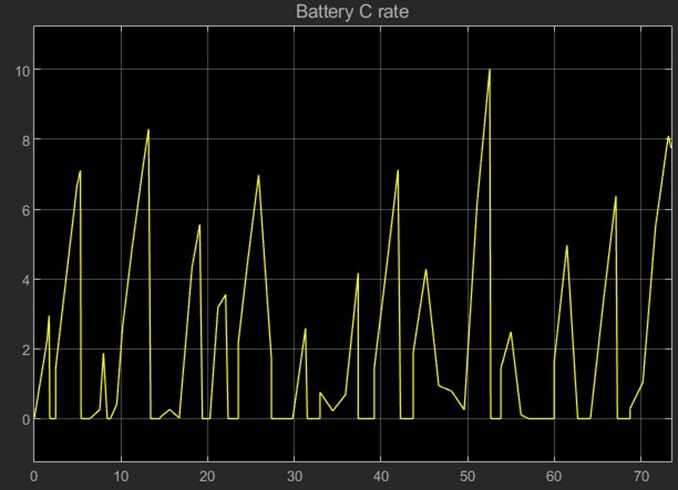
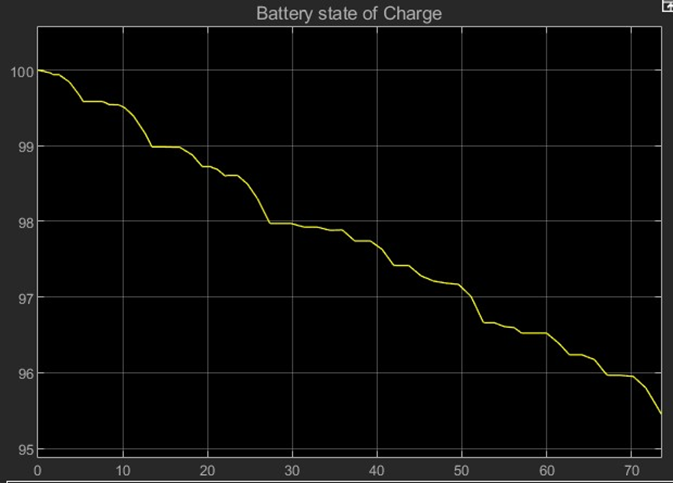
Key Takeaways
Through the process of developing the simulation, the team discovered that using MATLAB significantly saved time and effort, thanks to its exceptional speed and powerful capabilities. The software proved to be a versatile and efficient choice for solving a wide range of complex problems.
If you have any comments or questions about this project, feel free to reach out to us through LinkedIn or Facebook @ASU Racing Team!
- 범주:
- Automotive
댓글
댓글을 남기려면 링크 를 클릭하여 MathWorks 계정에 로그인하거나 계정을 새로 만드십시오.